Thermal Shock Chamber
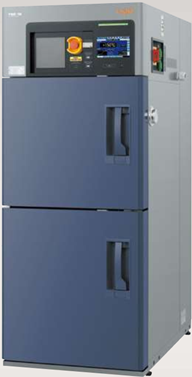
The TSE-12-A thermal shock chamber is used to test the reliability of a package when it undergoes a rapid change in a field or handling environment. Air to air thermal shock tests evaluates the reliability of test samples by repeatedly applying rapidly alternating high and low temperatures to them.
The expansion and contraction caused by the temperature variation generate stress from differences in the expansion rates of parts made of different bonded materials. Stress is also generated by differences in the heat capacity and thermal time constant of each component of the device.
The repeated action of stress causes accumulation of material fatigue, sometimes leading to rupturing at a lower strength than the static strength. Repeated stress can also cause bonded parts to crack, coatings to peel, and screws to loosen.
Typical Applications:
- Evaluating PCB mounting reliability after a change in lead-free solder or another connection material
- Evaluating reliability after a change in mounting format such as BGA or CSP
- Evaluating connection resistance by connector temperature variation
- Checking for cracks by thermal deformation of molded plastic parts
- Checking for cracking, peeling or seal leaks in bonded materials
- Evaluating combinations of different material types such as plastic with inserted nuts
Specifications:
- 2-zone transition by vertical transfer of specimen
- High temperature Exposure Range: +60 to +200oC
- Low temperature Exposure Range: -65 to 0oC
- Temperature fluctuation: +/- 0.5oC
- Recovery conditions:
- Hot exposure: +150oC, 30 min
- Cold exposure: -65oC, 30 min
- Specimen: 2 kg per basket (equally distributed)
- Temperature recovery time: within 5 min
- Transfer time between hot and cold chambers: within 10 sec
- Internal dimensions: W320xH148xD230mm